Understanding the Manufacture of Crankshaft: A Deep Dive into Diesel Engine Parts
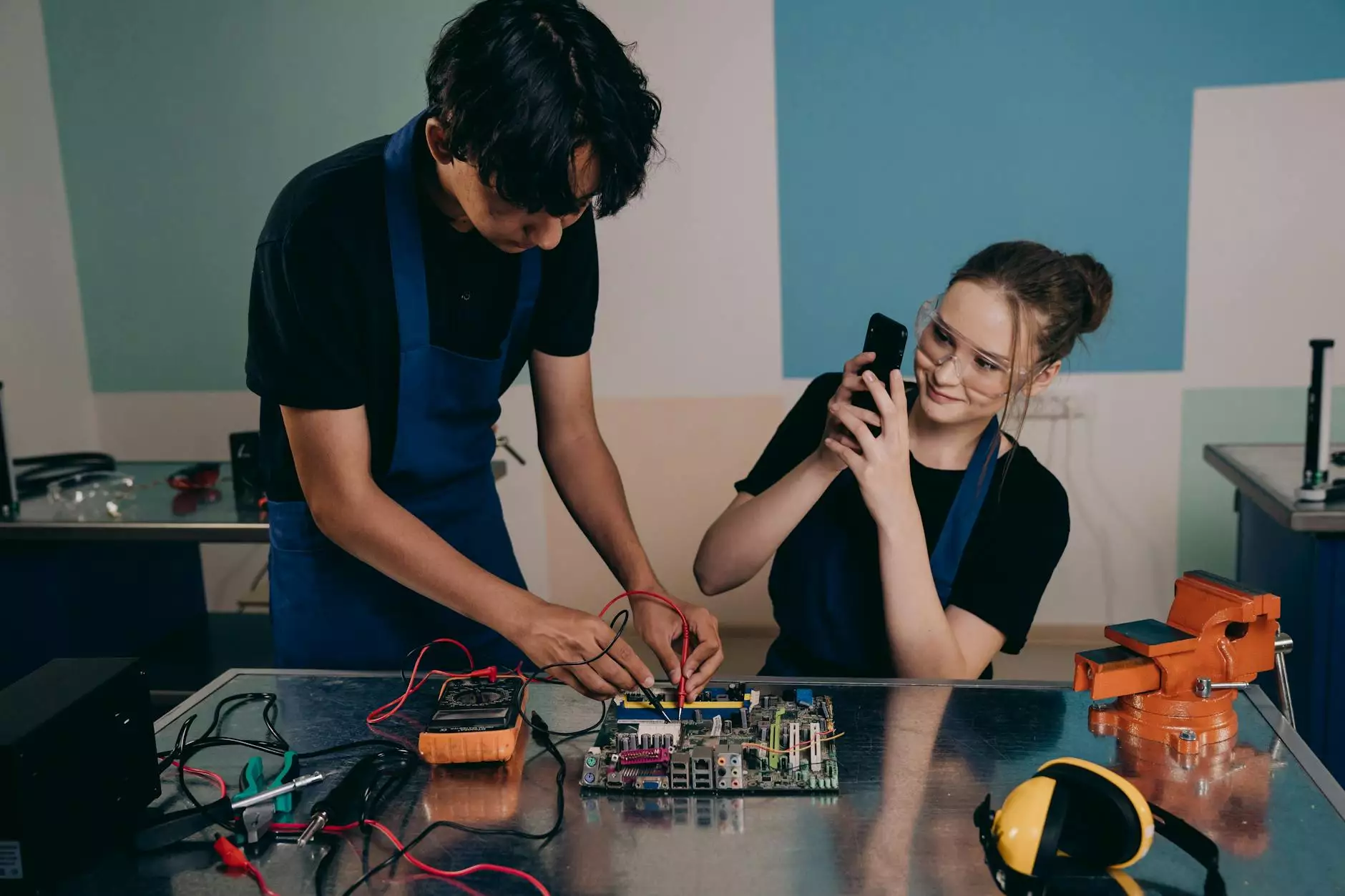
The manufacture of crankshaft is a pivotal component in the world of automotive engineering and specifically diesel engine mechanics. This article delves into the intricate processes involved in crankshaft production, its significance, and the implications for the overall performance of diesel engines. With the automotive industry constantly evolving, understanding these components is essential for businesses and consumers alike.
What is a Crankshaft?
The crankshaft is a fundamental part of any internal combustion engine. It converts the linear motion of the pistons into rotational motion, which ultimately powers the vehicle. The design and integrity of the crankshaft are crucial because any failure can lead to catastrophic engine damage.
Key Functions of the Crankshaft
- Power Conversion: The crankshaft is responsible for transforming the rectilinear movement of the pistons into rotational movement, providing the driving force for the vehicle.
- Balance: It helps maintain the engine's balance and reduces vibrations, contributing to a smoother performance.
- Support: The crankshaft supports several engine components, including the camshaft and connecting rods, requiring it to have robust structural integrity.
The Importance of Quality in Crankshaft Manufacture
In the manufacture of crankshaft, quality is not just an option; it is a necessity. High-quality crankshafts can significantly enhance the efficiency and durability of diesel engines. Here’s why quality matters:
Durability and Longevity
Quality materials and manufacturing processes extend the lifespan of the crankshaft, reducing the likelihood of failures that can lead to costly repairs. A well-manufactured crankshaft can withstand high stress and operate within optimal tolerances.
Performance Optimization
A precisely engineered crankshaft can lead to better fuel efficiency, increased horsepower, and less engine wear. These performance variations can significantly influence the operational costs of vehicles, especially in commercial applications.
Manufacturing Process of Crankshafts
The manufacture of crankshaft involves several detailed steps that ensure the best possible product emerges. Below is an overview of this complex process:
1. Material Selection
The process starts with selecting appropriate materials. Crankshafts are typically made from:
- Forged Steel - Offers superior strength and resilience.
- Cast Iron - A more economical option with excellent vibration dampening properties.
- Alloy Steel - Selected for high-performance applications requiring additional strength.
2. Forging
Once materials are selected, the next step is forging. In this step:
- The materials are heated to high temperatures and shaped into a rough crankshaft form.
- This process enhances the material’s structural integrity and is crucial for high-load applications.
3. Machining
After forging comes machining, where precision shaping occurs. The crankshaft undergoes various machining processes:
- Turning: Achieves the correct diameter and surface finish.
- Grinding: Ensures tight tolerances and smooth surfaces.
- Boring: Creates the necessary holes for oil passages and connecting rods.
4. Heat Treatment
Heat treatment is employed to harden the crankshaft further. This process helps improve wear resistance and overall durability.
5. Finishing Processes
The final stages include polishing and surface treatment to enhance corrosion resistance. This helps ensure that the crankshaft can withstand the harsh environments typically encountered in diesel engines.
Quality Control in Crankshaft Manufacture
Implementing a robust quality control process is vital in the manufacture of crankshaft. This process typically includes:
- Dimensional Inspection: To ensure that the crankshaft meets precise specifications.
- Material Testing: Conducting tests to assess the strength and quality of the materials used.
- Non-Destructive Testing: Techniques such as ultrasonic testing to detect internal flaws without damaging the crankshaft.
Notable Innovations in Crankshaft Manufacturing
As technology progresses, the manufacturing processes for crankshafts have also evolved. Some notable innovations include:
Advanced Materials
New research into composite materials could lead to lighter and stronger crankshafts, improving fuel efficiency and reducing emissions.
3D Printing Technology
This technology promises to revolutionize small-scale crankshaft production, enabling the manufacture of complex geometries that were previously impossible.
Choosing the Right Supplier for Crankshafts
For businesses looking to procure crankshafts, selecting a reliable supplier is crucial. Here are factors to consider:
- Reputation: Choose suppliers with a proven track record in manufacturing high-quality crankshafts.
- Certification: Ensure that suppliers meet industry certifications such as ISO 9001, which indicates quality management standards.
- Customer Support: A good supplier should provide excellent customer service, helping clients with technical questions and after-sales support.
The Role of Client-Diesel in Crankshaft Supply
For businesses in need of reliable diesel engine parts, client-diesel.com is an exceptional choice. Specializing in diesel engine parts and spare parts supply, Client Diesel prides itself on delivering quality and reliability.
Benefits of Partnering with Client Diesel
- Wide Selection: A comprehensive range of crankshafts and other diesel engine components.
- Competitive Pricing: Offering fair prices that reflect the quality of the products provided.
- Expert Knowledge: A team committed to providing clients with in-depth knowledge and support tailored to their needs.
Conclusion
The manufacture of crankshaft plays an essential role in the automotive sector, particularly in diesel engine technology. Understanding the manufacturing process, the importance of quality, and choosing the right suppliers, such as Client Diesel, can make a significant difference in the performance and longevity of diesel engines. As the industry continues to evolve, staying informed about innovations and best practices in crankshaft manufacture is crucial for ensuring optimal engine performance and reliability.
By prioritizing quality and innovation, businesses can benefit from enhanced efficiency, reduced operational costs, and improved customer satisfaction. As demand for high-performance diesel engines grows, so too does the need for exceptional crankshaft manufacturing. Choose wisely, and invest in the best.