How to Prepare Before a Quality Control Inspection
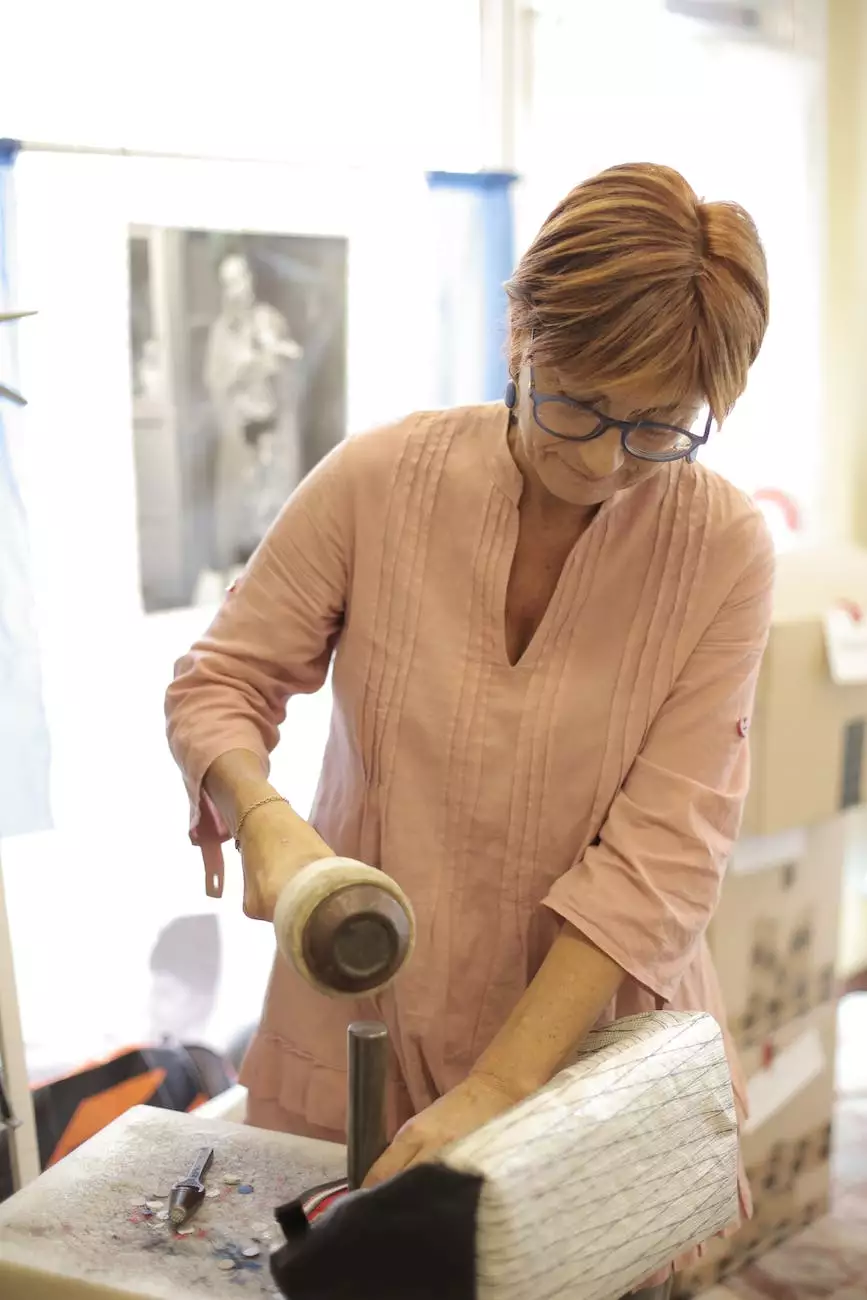
Introduction
Welcome to CTIP, The Council for Trade and Investment Promotion! As a reputable business and consumer services provider in the industry, we understand the importance of efficient and successful quality control inspections. This comprehensive guide aims to equip you with the necessary knowledge and strategies to prepare effectively before a quality control inspection. By following these steps, you can confidently navigate the inspection process and ensure optimal results for your business.
Understanding Quality Control Inspections
Before diving into the preparation process, it is essential to have a clear understanding of quality control inspections. Quality control inspections are a critical component of any business's operations, helping to ensure that products or services meet predetermined quality standards. These inspections typically involve thorough evaluations, tests, and assessments to identify any deviations from quality parameters. By proactively preparing, you can address any potential issues and prevent costly delays or rejections.
The Importance of Preparation
Preparation is key to a successful quality control inspection. It allows you to assess your operations, identify potential areas of improvement, and implement corrective actions beforehand. Effective preparation helps minimize risks, ensures compliance with regulations, and enhances overall product or service quality. By investing time and effort in adequate preparation, you can save resources, maintain your reputation, and gain a competitive edge in the market.
Step 1: Understand Regulatory Requirements
Prior to the inspection, it is crucial to familiarize yourself with the relevant regulatory requirements applicable to your industry. Research and understand the standards, guidelines, and regulations governing your products or services. This knowledge will enable you to align your operations with the necessary compliance measures. Stay updated with any changes or revisions to ensure ongoing adherence to regulatory standards.
Step 2: Document and Review Procedures
Documenting and reviewing your procedures is vital to ensure consistency and compliance. Review your existing procedures and identify any gaps or areas that need improvement. Develop comprehensive standard operating procedures (SOPs) that outline each step of your processes. These SOPs should be easily accessible to your employees, promoting consistency and reducing potential errors. Regularly update your procedures based on best practices and industry advancements to stay ahead.
Step 3: Perform Internal Audits
Internal audits serve as valuable assessments of your operations, allowing you to identify potential non-conformities and areas for improvement. Conduct regular internal audits to evaluate the effectiveness of your quality control systems and processes. Address any identified issues promptly and document corrective actions taken. This proactive approach will help you maintain a high level of quality and prevent surprises during the official inspection.
Step 4: Train and Educate Employees
Your employees play a significant role in ensuring the quality of your products or services. Proper training and education are critical to instilling a culture of quality within your organization. Offer comprehensive training programs that provide employees with a deep understanding of quality control principles, procedures, and expectations. Encourage open communication and a proactive approach to quality improvement. Regularly assess your employees' knowledge and skills to identify opportunities for additional training.
Step 5: Maintain Records and Documentation
Accurate and well-organized record-keeping is essential for a successful quality control inspection. Implement a robust system for capturing, maintaining, and organizing relevant records and documentation. This includes records of inspections, test results, corrective actions, and employee training. A comprehensive record-keeping system ensures easy retrieval of information during the inspection, demonstrating your commitment to quality and compliance.
Step 6: Conduct Mock Inspections
To prepare for the actual quality control inspection, consider conducting mock inspections. Mock inspections simulate the inspection process and help you identify potential gaps or weaknesses in your systems. Involve relevant stakeholders and subject matter experts to evaluate your procedures, documentation, and overall readiness. Address any identified areas of improvement promptly to strengthen your preparedness for the official inspection.
Conclusion
In summary, proper preparation before a quality control inspection is crucial for achieving optimal results. Understanding regulatory requirements, documenting procedures, performing internal audits, training employees, maintaining records, and conducting mock inspections are key steps in this process. At CTIP, as a leading business and consumer services provider, we are committed to helping you navigate through the inspection process successfully. By following the strategies outlined in this guide, you can enhance the quality of your operations, ensure compliance, and position your business for long-term success.